Hi all,
New member - based in the North West! I've been browsing for a while and getting a view as to what technology is available, and have drawn a few blanks. I'm looking to gauge some technical input on retrofitting electrical assist to a Lasher hand-cycle, which is an off-road only mountain bike which looks a little something like this:
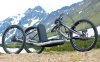
There are a number of technical considerations that have factored into the issue:
Secondly, a number of handcycles on the market or previously having been on the market use BionX, Bafang or Bosch systems. Whilst I have no doubt these are great I have seen a number of handcycle owners have issues with these systems when designs/interfaces/batteries etc have either been discontinued or they've just plain and simply gone bust lol and we just have no interest in dealing with legacy issues in the future, so we are absolutely happy to scratch produce everything (including the battery packs). We have CNC Plasma, TIG, mill, lathes etc at home and a full production capability for manufacturer of the mounting hardware and electrical equipment and stacks of Resin/FDM printers etc for other pieces.
We envisage currently taking the following strategy:

Cheers
Scott
New member - based in the North West! I've been browsing for a while and getting a view as to what technology is available, and have drawn a few blanks. I'm looking to gauge some technical input on retrofitting electrical assist to a Lasher hand-cycle, which is an off-road only mountain bike which looks a little something like this:
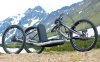
There are a number of technical considerations that have factored into the issue:
- The bike has a Rohloff Speedhub on the front, so there is no desire to change to a hub motor at all.
- Handcycles are notoriously slippy on the front as all the weight sits on the rear, so there is little desire to fit a mid-drive.
- The bike has no rear brakes or mounts on the rear axles and uses 1/2" push-fit axles and wheelchair wheels.
- There is no aspiration for pedal assist, but only for a thumb throttle to assist with standing starts on flat and to provide assistance when required on steeper off-road sections.
Secondly, a number of handcycles on the market or previously having been on the market use BionX, Bafang or Bosch systems. Whilst I have no doubt these are great I have seen a number of handcycle owners have issues with these systems when designs/interfaces/batteries etc have either been discontinued or they've just plain and simply gone bust lol and we just have no interest in dealing with legacy issues in the future, so we are absolutely happy to scratch produce everything (including the battery packs). We have CNC Plasma, TIG, mill, lathes etc at home and a full production capability for manufacturer of the mounting hardware and electrical equipment and stacks of Resin/FDM printers etc for other pieces.
We envisage currently taking the following strategy:
- Retrofitting of a drive motor to either one or two of the rear wheels.
- Use of a CAN communication system between two VESCs on the rear if required.
- Use of a standard FRONT disc mount ready Hope Pro 4 type hub and suitable 26" rim on each side at the back with suitable adapters to match the push fit nature of the frame.
- Fitment of "fixed gear bike" style disc mount chain sprockets onto the hub.
- Fitment of a suitable motor onto the frame either through a TIG welded mount or our preference of a STAUFF clamp and torque control arm (it would be nice to be able to remove the entire setup sometimes!)
- Fitment of a suitable battery pack (likely 48v?) on the rear end of the bike to suit.
- Given the above specification, can anybody recommend a speed controller that will simply allow us to run a thumb throttle with the minimum amount of fuss?
- We had considered this: https://www.4qd.co.uk/product/porter/ but it doesn't look like we will be able to use this with alot of the motor tech currently out there?
- Can anybody recommend a motor technology which will allow us to ensure the motor adds no drag when not being used?
- We had considered BLDC but ideally just want something easy to package, where we can easily fabricate some mounts and put a simple chain wheel or toothed belt sprocket on without too much fuss!
- Can anybody recommend a motor and controller combo which might fit our needs?
Cheers
Scott