My Reprogrammed Settings-NOT guaranteed in any way!
BBS02 36v 500w 25A with 36v 18AH. Battery is 60 x 30Q Samsung cells. (10s6p)
The bike is a 2004 Gary Fisher 29er hardtail. Gross bike weight is 19 kilos. I weigh 72 kilos.
10 speed cassette 11-34. 42t chainring.
Display settings. PAS levels 5. Wheel diameter 700c. Max Speed 50kph
No Throttle fitted. Standard brake levers.
I found the standard controller settings felt very odd. The bike would give a massive push from a standing start and then the motor would back off once up to speed and pedal cadence above 70rpm or so. It felt over governed sometimes going too fast like it was on cruise control, other times I had to pedal very hard to maintain a given speed. With the standard settings I was getting around a 36 mile range from the battery before I noticed a drop off in performance. In PAS level 3, the bike would hack along at 25mph, but getting up to 26mph was nigh impossible. PAS Level 2 was more comfortable with the speed being around 18.5mph, but to go any faster I had to push very hard or change to PAS3 when it took off to 25mph again. The motor also kept spinning when I stopped pedalling which I found very disconcerting. (I don’t use the Bafang sensor brake levers)
I aim is to make the motor behave in a more predicable way, delivering power throughout the speed and cadence range. I read all of the stuff regarding reprogramming the controller on the internet and while most is good advice, I have arrived at a slightly different solution.
The reprogrammed settings I‘ve been running for the past week or so feel much better. The motor keeps delivering power even at high cadence. I have to use the gears more, just like riding a normal bike, except I’m putting in about half the effort (compared with a normal bike) for a given speed/gradient.
With 5PAS levels, I find that I use PAS level 2 most of the time, only using PAS3 if climbing a long hill or into a strong headwind. Used PAS 5 briefy on a fast flat section with a slight tailwind. I hit 38mph before the 120rpm + cadence was too high for my current fitness level to maintain. If I’d had a bigger gear I could have hit a higher speed. Not bad for a mountain bike! Based on guesswork the BBS02 was producing about 460 watts (assuming 80% efficiency) add my 300watts = 760watts, this sounds about right to me, given that power vs speed is not linear.
Based on my settings the motor will peak at 4.64 amps in PAS 2 and 7.68 amps in PAS 3. This seems to fit with my power (wattage) readings on a normal bike. I was able to push an average of 300 watts for 30 mins or so on my road bike. (Ok not quite up to the 500watts of professionals but average for a club cyclist)
Range has improved, alough its early days yet. I’ve done 32 miles on a charge so far. I’ll check the battery voltage before I go out again, but I’m hoping to manage a 20 mile ride this evening giving me range of 52 miles. I’d be interested to compare range with others experiences. Maybe we should use hours and minutes rather than range in miles to take into account different terrain on/off road etc? I’m hoping to get over 3hrs from the battery at an average speed of 17.5 mph on rolling roads with some single track.
I’m not overly worried about frying the controller since I’ve limited max current to 16 amps and in PAS 2 I’m only using 29% of the 16 amps and in PAS 3 only 48%. Remember I’m using 5 PAS levels. I also keep cadence above 75rpm by using the gears which minimises the load on the motor. . Maybe the controller and BMS allow more current for a short while, I’m not sure.
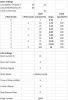
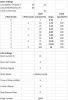