After adding two of the cheapo torque arms on my rear hub and redoing mechs so everything fitted together better (I think local bike guy tried to kill me on at least three occasions past cpl years..), I'd gotten a little cocky and stopped checking the rear hub before each trip.
Anyway it spun out the other night there, both torque arms did I suppose eventually their job and stopped axle falling out of dropouts however nuts both side were hand loose and the left side was getting close to edge of dropouts. The cable from hub axle to connector to battery got caught and damaged although it wasn't pulled out the controller socket.
Had designed a 3d printed torque arm but had been too lazy to get it metal cut as thought the two cheap torque arms would suffice...with hindsight...
Shield was torn and you can see green phase power wire shielding is damaged. My understanding is that I have 9 wires in total:
Thick blue/green/yellow wires are phase power
Thin blue/green/yellow wires are phase sensors
Red/Black is +ve/-ve for motor board
White is speed sensor
(No 10th thermistor wire)
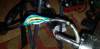
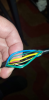
Controller is this (17A continuous, 35A peak).
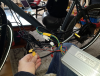
Display:
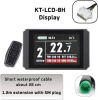
When I power on no error on display however when I push thumb throttle I get this error so assumption is that wiring is damaged either in the hub harness cable or actually inside the motor and shorting. If it was thick wires I might expect smoke but not for thin wire sensor short but could be the red/black power? I dunno.
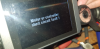
When I unplug the hub and use throttle I get this error which I've seen before when I was fitting in USB C and knocked lose the thin wire connector so this error is to be expected when hub is not plugged in?
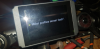
So any suggestions as to way forward?
Probably I will have to strip off all the shielding to check wires however if it's inside the hub then it will be going in the bin (never bought the big gear puller in end as I like 10 fingers). I got bearing redone few months ago then the fecker started clicking again few weeks ago, have been thinking of downgrading hub however I would like to understand if there are any suggested tests I can do to try and narrow down issue? I can check sensor wires by manually spinning wheel and probing controller, what else can I test? I'm assuming the controller will be OK as it has short circuit protection.
Any thought welcome. Thanks
Anyway it spun out the other night there, both torque arms did I suppose eventually their job and stopped axle falling out of dropouts however nuts both side were hand loose and the left side was getting close to edge of dropouts. The cable from hub axle to connector to battery got caught and damaged although it wasn't pulled out the controller socket.
Had designed a 3d printed torque arm but had been too lazy to get it metal cut as thought the two cheap torque arms would suffice...with hindsight...
Shield was torn and you can see green phase power wire shielding is damaged. My understanding is that I have 9 wires in total:
Thick blue/green/yellow wires are phase power
Thin blue/green/yellow wires are phase sensors
Red/Black is +ve/-ve for motor board
White is speed sensor
(No 10th thermistor wire)
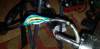
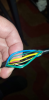
Controller is this (17A continuous, 35A peak).
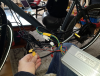
Display:
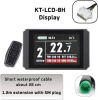
When I power on no error on display however when I push thumb throttle I get this error so assumption is that wiring is damaged either in the hub harness cable or actually inside the motor and shorting. If it was thick wires I might expect smoke but not for thin wire sensor short but could be the red/black power? I dunno.
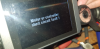
When I unplug the hub and use throttle I get this error which I've seen before when I was fitting in USB C and knocked lose the thin wire connector so this error is to be expected when hub is not plugged in?
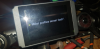
So any suggestions as to way forward?
Probably I will have to strip off all the shielding to check wires however if it's inside the hub then it will be going in the bin (never bought the big gear puller in end as I like 10 fingers). I got bearing redone few months ago then the fecker started clicking again few weeks ago, have been thinking of downgrading hub however I would like to understand if there are any suggested tests I can do to try and narrow down issue? I can check sensor wires by manually spinning wheel and probing controller, what else can I test? I'm assuming the controller will be OK as it has short circuit protection.
Any thought welcome. Thanks