Brompton - Cycle Analyst & Thun Torque Sensor Installation (Part 1)
I installed a Freedom Ebikes kit on my white Brompton in mid-2012. The original Tongxin motor worked well and I had no problems with it. At some point, I replaced the original controller with a KU63 from BMSBattery.com and that whole setup served me well for more than a year and a half.
A few months ago, I started to take the mods further and replaced the Tongxin motor with a smaller Keyde motor as well as installed a Cycle Analyst unit together with a Thun bottom bracket torque sensor. And to make the whole setup as stealthy as possible, I hid the two 2.3Ah 6S LiFePO4 packs and the KU63 controller within the frame of the Brompton Folding Basket.
Keyde motor swap
The replacement Keyde front hub motor (250W/260rpm/36V/28-hole) weighed in at about 1.45Kg (compared with 2.1Kg for the Tongxin). I got rid of the CR18 rim (thank God for that) and laced the motor with a new 2013 Brompton double-walled rim. I bought the angle-drilled version of the rim which works well with a 1-cross or 2-cross lacing. There is no spoke bending at the nipples at all. I ordered the 13-gauge spokes from BMSBattery.
FET anti-spark switch and charging harness
I used Jeremy Harris’ simple FET switch circuit with three IRFB4110 FETs in parallel. The components were soldered on a 1.5” x 0.6” piece of perf board and it, in turn, was wired to a small switch, battery connectors and charging connectors. With the switch in the one position, the battery pack is connected to the controller. In the other position, the battery is connected to the charging connectors. One IRFB4110 would have been fine for the KU63’s 15 Amp limit. But I decided to use three in parallel because I suspected that the FETs I bought were bootlegs and would likely have a higher RDS(on) resistance than the real ones. However, I found that the FETs were barely warm in normal usage. So two (or even one) would have been sufficient, in retrospect.
Concealed battery and controller
The two 6S LiFePO4 2.3Ah packs, the KU63 controller, FET switch harness and the Cycle Analyst current shunt were wired and strapped to the aluminium frame of the Brompton Folding Basket. The frame slips back into the Folding Basket and everything is concealed. Connection from the Folding Basket electronics to the bike was via a 9-pin connector — the same type used for connecting sensored motors to a controller. I chose this type of connector because it had the required 3 big conductors for motor power and the 6 signal conductors required by the Cycle Analyst. Slim and waterproof too.
<Continued on next post>
I installed a Freedom Ebikes kit on my white Brompton in mid-2012. The original Tongxin motor worked well and I had no problems with it. At some point, I replaced the original controller with a KU63 from BMSBattery.com and that whole setup served me well for more than a year and a half.
A few months ago, I started to take the mods further and replaced the Tongxin motor with a smaller Keyde motor as well as installed a Cycle Analyst unit together with a Thun bottom bracket torque sensor. And to make the whole setup as stealthy as possible, I hid the two 2.3Ah 6S LiFePO4 packs and the KU63 controller within the frame of the Brompton Folding Basket.
Keyde motor swap
The replacement Keyde front hub motor (250W/260rpm/36V/28-hole) weighed in at about 1.45Kg (compared with 2.1Kg for the Tongxin). I got rid of the CR18 rim (thank God for that) and laced the motor with a new 2013 Brompton double-walled rim. I bought the angle-drilled version of the rim which works well with a 1-cross or 2-cross lacing. There is no spoke bending at the nipples at all. I ordered the 13-gauge spokes from BMSBattery.
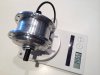
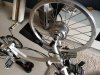
FET anti-spark switch and charging harness
I used Jeremy Harris’ simple FET switch circuit with three IRFB4110 FETs in parallel. The components were soldered on a 1.5” x 0.6” piece of perf board and it, in turn, was wired to a small switch, battery connectors and charging connectors. With the switch in the one position, the battery pack is connected to the controller. In the other position, the battery is connected to the charging connectors. One IRFB4110 would have been fine for the KU63’s 15 Amp limit. But I decided to use three in parallel because I suspected that the FETs I bought were bootlegs and would likely have a higher RDS(on) resistance than the real ones. However, I found that the FETs were barely warm in normal usage. So two (or even one) would have been sufficient, in retrospect.
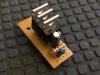
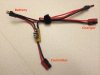
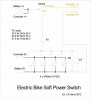
Concealed battery and controller
The two 6S LiFePO4 2.3Ah packs, the KU63 controller, FET switch harness and the Cycle Analyst current shunt were wired and strapped to the aluminium frame of the Brompton Folding Basket. The frame slips back into the Folding Basket and everything is concealed. Connection from the Folding Basket electronics to the bike was via a 9-pin connector — the same type used for connecting sensored motors to a controller. I chose this type of connector because it had the required 3 big conductors for motor power and the 6 signal conductors required by the Cycle Analyst. Slim and waterproof too.
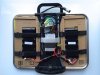
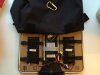
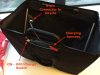
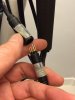
<Continued on next post>